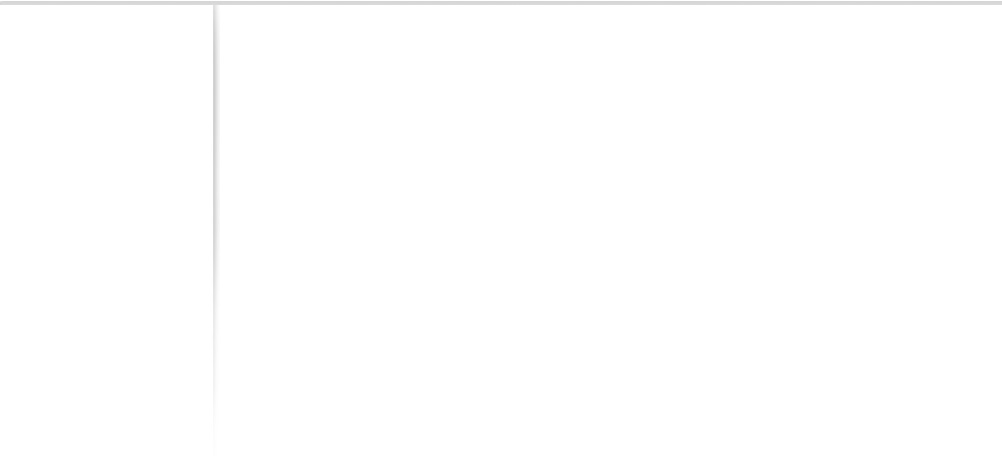
一,问题的提出。
批量生产同一产品的二级斜齿圆柱齿轮减速机,有的噪声较低且传动较平稳,听感很正常,有的则产生唰啦唰啦响的间歇性高噪声,听起来很烦人。
笔者深入生产车间进行了考察,测试,分析和改进试验,用ND6型精密声级计测试,低噪声减速机为79.8dB(A),达到了出厂要求。而高噪声减速机为82.5dB(A),达不到出厂要求,需要进行降低噪声的治理。
二,噪声源分析。
对高,低噪声减速机运转后拆开上盖观察比较,如图1所示。低噪声减速机的齿面接触精度很高,整个齿面上都有接触斑痕,而高噪声减速机的第一级齿轮轴1与齿轮2接触精度比较低,接触斑点达不到50%,即轮齿在齿宽方向上,齿面边缘一端有接触斑痕(即咬边),其另一端齿面边缘无接触斑痕(即不咬边),造成轮齿在其接触宽度上不完全啮合。第二级齿轮接触精度都很高。可见噪声源在第一级齿轮上,即使在同一台滚齿机上一次调整滚刀角度加工这一对齿轮也会出现咬边,排除了机床误差的影响。
对产生咬边现象的原因进行分析。
1.轴3加工误差分析。
为保证加工精度,其轴颈,轴肩与齿轮内孔配合部分均在精研轴中心孔后的统一基准上一次磨削,磨床精度良好,加工件装配后不会引起齿轮的咬边现象。
若磨削规范选择不当,仍有可能产生轴颈磨后的径向跳动。
轴3与齿轮内孔配合选取H7/k6,配合比较紧,不会引起齿轮咬边。
2.箱体孔不平行。
箱体孔是在刨削箱体各平面后,上,下箱体装配成一体在卧式镗床上分粗镗,半精镗和精镗加工的,用单面前导向一次镗出两边孔。经检验,镗床和镗模精度良好,能保证箱体孔平行度,不会引起齿轮咬边。
箱体铸造后清砂,去分型面处的夹边和冒口,喷丸处理后时效处理4个月,消除了内应力,加工后无变形,不会引起齿轮咬边。
3.齿轮加工误差分析。
滚刀刃磨及对中很好,用一把新滚刀加工,也和原有滚刀一样出现一级变速齿轮咬边现象,刀具原因可排除。
齿坯内孔与端面是在同一次装夹中完成加工的,保证了垂直度。
在心轴上用内孔和端面定位,经计算无过定位现象,内孔与心轴的配合满足定位误差要求,不是产生咬边的原因。
滚刀在滚刀架主轴上安装,对滚刀两端台肩的径向跳动应控制在0.1mm以内,台肩端面跳动应控制在0.005mm以内。
4.工艺系统受力变形。
如图3所示为在滚齿机上滚切齿轮轴1的安装示意图,轴1左端向上,用顶尖定位,另一端向下用三爪卡盘定位和夹紧,整个齿轮轴相当于一根上端铰支,下端简支的梁,且顶尖至齿轮的距离202mm,大于齿轮至三爪卡盘的距离125mm,因此,对齿轮来说,上端受力变形大,所切齿深就浅;而下端受力变形小,齿深就深。
在滚齿机上用心轴定位滚切齿轮2的安装示意图,心轴上端在轴承中相对转动,又用顶尖压紧,心轴下端在锥孔中定位,整个心轴相当于一根两端简支的梁,且心轴上端长度71mm比下端长度210mm小得多,心轴下端直径为32mm,而上端直径56mm,因此,上端刚度比下端大,对齿轮来说,上端受力变形小,切出的齿深就深;而下端受力变形大,齿深就浅。由于该齿轮的中性面对称,装配时会任意装配,就使两齿轮齿浅的一端装配在同一端,出现咬边现象而产生噪声。
三,噪声治理及其效果。
综上所述,齿轮传动的噪声由齿轮箱主要零件的设计,制造和装配质量等因素所决定的,找到原因后,研究解决的措施如下。
1.从加工工装上解决。
重新设计工装,消除受力变形,但不经济。
2.采用误差抵消法。
齿轮的下端面即主要定位基准做装配基准,齿轮2的右面,这样齿轮2齿浅(深)
端正好与齿轮轴1的齿深(浅)端啮合,误差抵消。
对高噪声减速箱重新采用误差抵消法装配后,其降低噪声效果即可立杆见影,噪声降为79.8dB(A),传动平稳且噪声低,无唰啦响的间歇性噪声,达到了出厂要求,用户很满意。