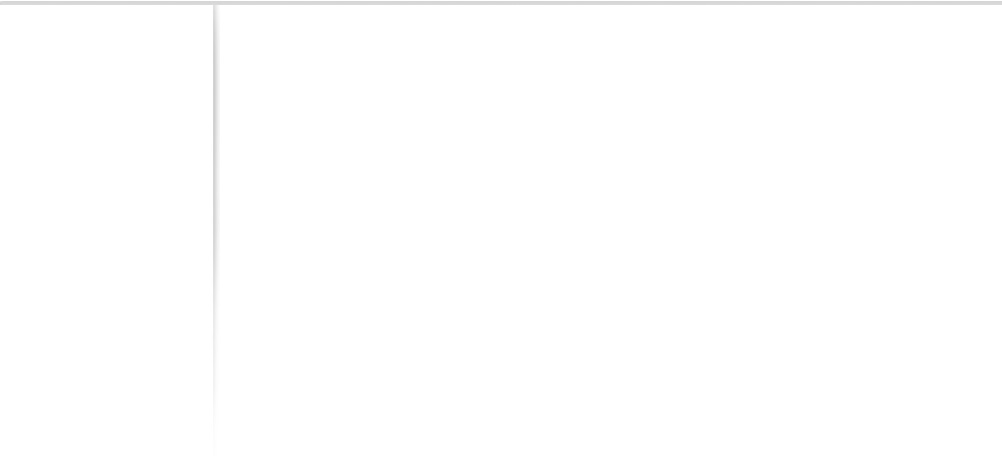
1概述
铸造起重机是冶金厂的专用起重设备,主要为炼钢厂转炉或电炉服务,用于吊运熔化金属,具有工作频繁,负荷作业率高,工作条件恶劣,速度高等特点。铸造起重机的机械部分主要有起升机构,起重机及小车运行机构,各机构的主要部件为传动系统,减速器是传动系统的重要单元。在整个起升机构中,减速器承担着传递动力,实现工况速度的重任,起重机用减速器是起重机设备专有的配套设计和制造技术,是起重机安全可靠运行的重要保障。
一般减速器都采用底座式结构,即底座平面和机体剖分面平行,镗孔时以底座平面作基准。
起重机是一个钢结构的整体,其变形量是一个很可观的数字,而减速器本身不允许变形,这样就要求减速器的安装位置能克服机构本身的变形。
2铸造起重机主起升机构传动型式
建国初,国内起重机减速器长期以来是以前苏联PM减速器系列为主改型的国产的ZQ系列减速器。20世纪80年代,国内主要采用的是西德在MAN公司减速器系列的基础上,制定出的DIN15053国家标准减速器。
目前国内使用的铸造起重机,其主起升机构的传动方式,大致可分为"品"字型三减速器传动型式和硬连接的传动型式二种。
传统的"品"字型三减速器传动型式,轴向结构尺寸较大。通常一级减速器内都带有行星或棘齿轮机构保证两输入轴的同步,每两级减速器之间通过联轴器传递力矩,传动环节多,制造成本较高。从理论上来讲,单减速器卷筒在外的布置形式要比卷筒在内的布置形式受力更合理,但变形对减速器的使用造成的影响未经实践证明,因而齿轮啮合间隙有待于通过试验获取相关数据,确立数据模型,以使设计更加合理,可行。目前,国外同类铸造起重机的主起升机构中,均采用传统的品字型三减速器传动型式和卷筒在内的布置型式的技术。
3新型单减速器传动理论设计
此次设计的铸造起重机,用于炼钢厂用于吊运铁水。起重机要求为四梁四轨,铰接端梁结构型式。主要由桥架,主小车,副小车,大车运行机构,司机室及检修吊笼装置,电气控制系统等部分组成。主小车沿着主梁轨道运行,副小车沿着副主梁轨道在主小车下面运行,整车沿着厂房轨道运行。
主小车起升机构采用两电动机,四个盘式制动器,一件减速机,并列式布置驱动,该减速器在高速轴通过齿轮相连,能确保起升机构在一台电机和它所配制动器故障时,可由另一台电机驱动,完成一个工作循环。在盘式制动器上设有手动释放装置,能确保在制动器故障时,可用该装置将制动器打开,保证机构能完成所剩余的工作。
在设计时,主起升机构在司机室对侧的极限尺寸很小,为确保不与厂房上料管干涉。必须设计一种结构紧凑的新型传动方式。本设计首次采用单减速器卷筒在外的布置。这种布置方式,其轴向结构尺寸小于品字型三减速器传动方式,吊点距方向结构尺寸小于两个卷筒放在减速器中间的布置型式,同时取消了常用的行星或棘齿轮机构,直接通过两高速级之间的同步齿轮来实现两卷筒之间的同步动作。这种结构的使用大大降低了制造成本以及传动链的传动环节,同时直接减小了整车极限尺寸。
在设计时,将减速器机体设计成刚度相对较高的双幅板结构,减速器机体刚度高于小车架刚度。当额定负荷工作,小车架出现下挠时,由于减速器机体刚性较高,并不随着小车架的下挠而产生变化,同时减速器产生相应的应力。
减速器与小车架之间的固定方式采用单侧固定,另一端游动的方式。当小车架下挠时,未拧紧的减速器一侧将沿着导向块在底座上滑动,从而避免减速器中心距发生变化。在此理论基础上可以初步确定,该小车架的下挠不足于影响齿轮啮合间隙。
从理论上来讲,这种传动方式结构紧凑,受力更合理。但由于采用单减速器,减速器自身体积增大,传动环节增多,这样就可能在工作中引起减速器的剧烈振动和较大变形,产生较大的冲击载荷。为了评价这种传动方式的可靠性,合理性和科学性,以使今后的设计更趋完善,对其进行有限元分析。
4有限元分析
对铸造起重机主小车架和减速器的壳体进行有限元分析,确定其应力和挤压应力的分布,为产品设计和齿轮啮合间隙的选取提供可靠的分析数据。
4.1边界条件该铸造起重机小车架为钢结构件,主减速器通过螺栓一头固定在小车架上,另一头游动。起吊载荷过程中,减速器与小车架呈刚性联接,但由于其刚度不同,所以壳体上内力分布并不均匀,主要表现为输出轴承座正下方呈挤压应力状态。
小车架,减速器上下壳体均为钢板焊接而成,小车架为箱形框架梁,腹板和上下盖板以及减速器下壳体用槽钢和钢板进行了加强,小车架上部承受起吊小车及设备重量,下部通过两边的车轮与轨道接触。这样,小车架梁的内力大多为复杂应力状态,既承受弯曲,扭转,又承受外力作用的局部压力。减速器下壳体承受着全部减速器自重以及同时将减速器上承受的压力传递到小车架上。
本体部分采用能反映平面变形和弯曲变形的壳单元,减速器出轴处为实体六面体单元,共有13680个节点,13860个单元,计算规模为72080个自由度。
4.2计算分析由于钢板多为复杂应力状态,在额定载荷下用第四强度理论等效应力云图计算各部位变形规律。
小车架以及减速器下壳体最大应力均小于材料屈服极限,具有足够的安全系数。小车架以及减速器下壳体应力集中处区域很小,即使有很大的冲击载荷作用使局部屈服,高应力区域将随着扩大,小车架及减速器下壳体承载能力也会相应增强,所以,从静强度破坏的角度来看,这一类型的应力影响较小,远小于材料屈服极限。
通过有限元模拟分析,可以计算出在工作载荷作用下时,减速器中心的最大垂直位移为0.033 mm,水平方向位移为0.0018μm.这一数值远远影响不到电机轴上两个齿轮间的啮合精度。
4.3减速器及小车架变形试验检测及分析试验检测在实际的生产情况下进行。在加载为额定载荷时,稳定情况下检测减速器两输出轴间的位移和小车架梁的强度和挠度;在加载0.8倍额定载荷时,载荷以最大速度起升时,检测减速器的振动情况。检测后对结果进行处理分析如下:1)速器外观质量现状良好。运转平稳,箱体严格密封,防尘,润滑条件好,壳体具有足够的强度和刚度。
2)减速器两输出轴的位移很小。正常工作情况下最大为0.09mm,比理论计算值0.066mm稍大。结合小车架的下挠情况分析,可以看出小车架的变形基本不影响减速器两输出轴的位移。
3)小车架梁最大下挠为f=3.2mm,与理论计算值相比f<4.14mm,满足设计要求。小车架梁最大应力为σ=13.2MPa,按照线性关系计算,可得出在满载时最大应力σmax=16.1MPa,与理论计算值相比,远小于σ=98MPa,可见有足够的安全裕度。
4)减速器输入轴最大振动加速度为0.18g(测量间接值);输出轴最大振动加速度为0.20g,最大振幅为65μm.振动加速度很小,振幅满足标准小于80μm的要求,说明该减速器各级传动灵活,齿轮啮合正常。初步可以认定该减速器机体刚度设计合理,小车架刚度可行时,这种传动方式中减速器中心距虽然发生变化,但并没有影响到两个同步齿轮间的啮合精度。
5结论
单减速器卷筒在外的布置型式,轴向结构尺寸小于品字型三减速器传动方式,吊点距方向结构尺寸小于两个卷筒放在减速器中间的布置型式,同时取消了常用的行星或棘齿轮机构,直接通过两高速级之间的同步齿轮来实现两卷筒之间的同步动作。这种结构的使用大大降低了制造成本以及传动链的传动环节,同时直接减小了整车极限尺寸。
经过有限元分析计算和变形试验检测可知:该起重机起升机构传动方式设计合理可行;在该设计结构型式下,小车架的变形对齿轮啮合精度并未造成质的影响和产生振动。同时由于减速器机座刚度的合理设计,减小了小车架的变形量,提高了小车架的使用寿命。